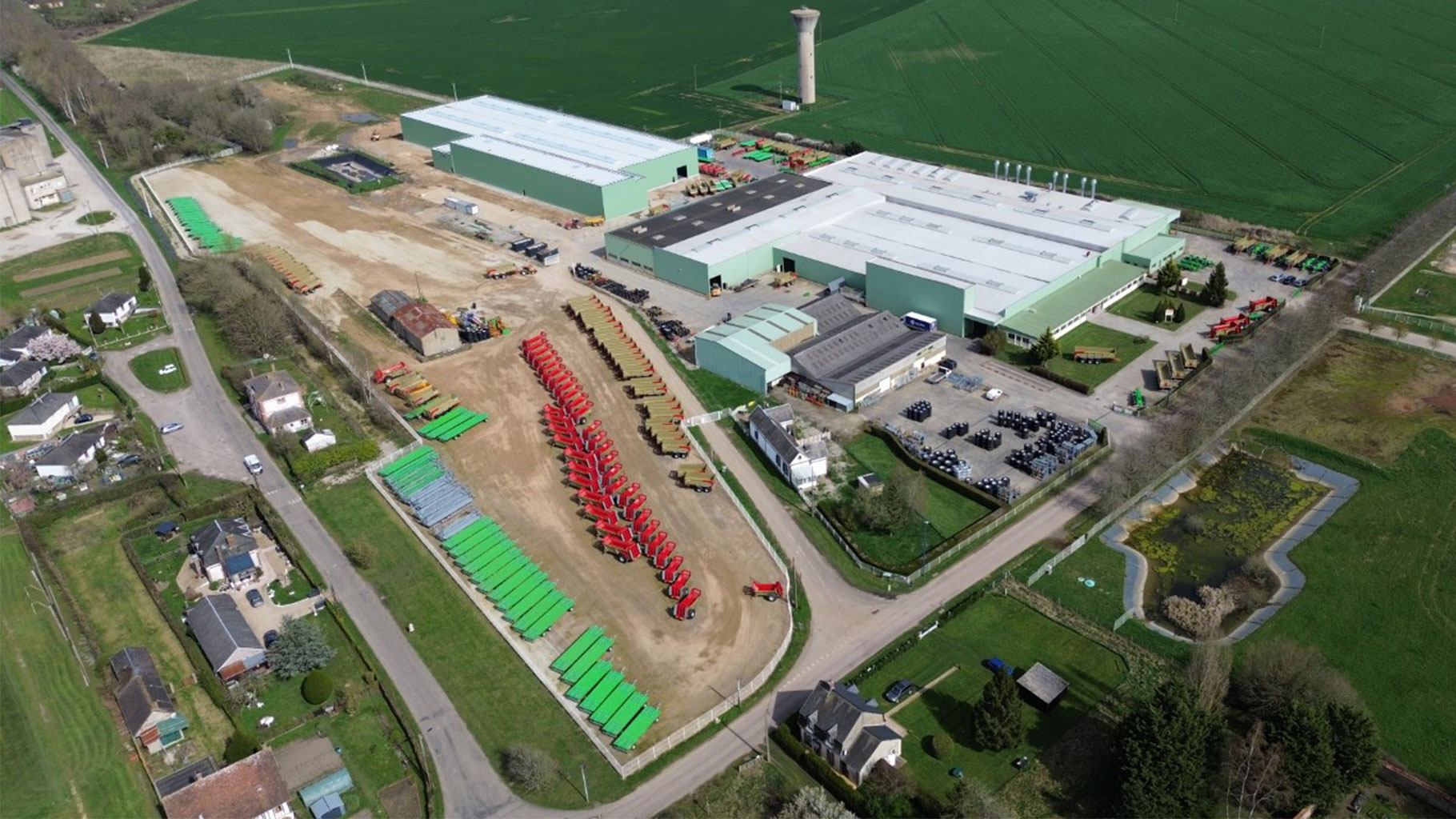
1921
Company foundation
21 000 m²
Factory size
46
Staff
310
Number of Leboulch machines produced
Leboulch group
At the cutting edge of technology
In order to offer you the best agricultural machines, our factory is equipped with state-of-the-art, high-precision tools from the first to the last production stage.
In-house research and development
Cutting-edge production technology
Quality materials
Made in France
Know-how for over 100 years